A workplace ergonomic intervention involves several steps to identify, analyze, and enhance working conditions. Here is a standard process applicable to both small and large projects as well as the services offered.
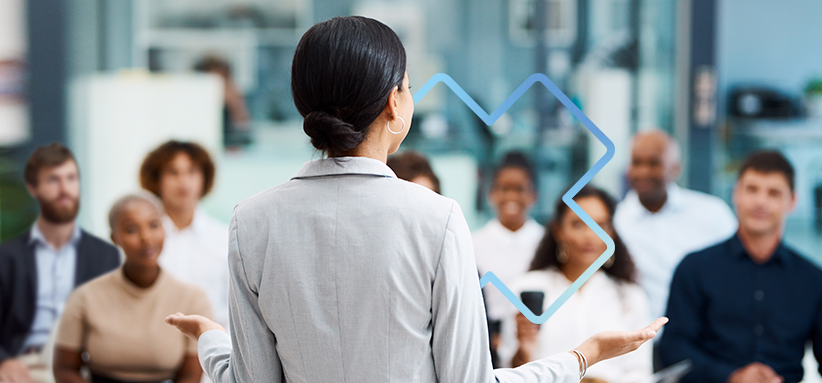
Our approach
Request analysis
- Meeting with management, supervisors, and workers
- Defining objectives (reducing musculoskeletal disorders (MSDs), improving productivity, safety, well-being, etc.)
- Establishing the methodology, project timeline, budget, and project team
Workplace observation and data collection
- Visiting the company and observing work processes
- Conducting interviews with operators and managers to understand challenges
- Analyzing accident data if necessary
- Collecting quantitative and qualitative data (measurements, videos, questionnaires, etc.)
Data analysis
- Studying worker movements, postures, and workflow
- Identifying physical constraints (efforts, repetition, vibrations, etc.)
- Evaluating cognitive constraints (decision-making, attention, stress)
- Assessing environmental factors (lighting, noise, temperature, etc.)
Diagnosis and problem identification
- Summarizing observations and identifying risk factors
- Analyzing discrepancies between prescribed work and actual work
- Prioritizing issues based on their impact
Solution development and testing
- Co-developing solutions with the company team
- Prototyping or simulating improvements
- Testing solutions over a trial period
Implementation and follow-up
- Validating the selected solutions
- Supporting operators in adopting new practices
- Providing training and raising awareness if necessary
- Adjusting solutions as needed
A real-work analysis ensures that improvements are tailored to both worker and company needs.
Services offered
Identification of Ergonomic Risks
A detailed assessment is conducted to identify risk factors related to:
- Repetitive movements and prolonged postures,
- Improper use of equipment or tools,
- Physical strain from manual handling,
- Psychosocial and organizational factors that influence work methods.
This critical step provides a clear understanding of potential issues and helps prioritize interventions.
Implementation of Ergonomic Solutions
Once risks are identified, our experts work with your team to:
- Redesign workstations,
- Recommend equipment or tools suited to employees' tasks,
- Train employees on best practices and risk reduction strategies,
- Implement organizational changes to minimize exposure to risks.
Continuous monitoring and evaluation
Ergonomic risk prevention is an ongoing process. Our experts assist companies in monitoring improvements through measurement tools and regular audits to refine interventions as needed.
Why Choose Us for Ergonomic risk management?
- Recognized expertise: Our interventions are based on proven practices and years of experience.
- Tailored approach: Every workplace is unique, and we customize our solutions to your specific needs.
- Proactive vision: We help you anticipate problems before they arise, ensuring a safe and efficient work environment.
Benefits for Your Organization
- Cost reduction: Less absenteeism and fewer injuries thanks to effective prevention.
- Increased productivity: Healthy employees are more engaged and efficient.
- Enhanced job satisfaction: An ergonomic workplace promotes employee well-being and retention.
Contact us
Want to prevent ergonomic risks in your organization and create a healthy, productive work environment? Contact us today to schedule a customized assessment.